Want to boost profits? Build sustainability into your business
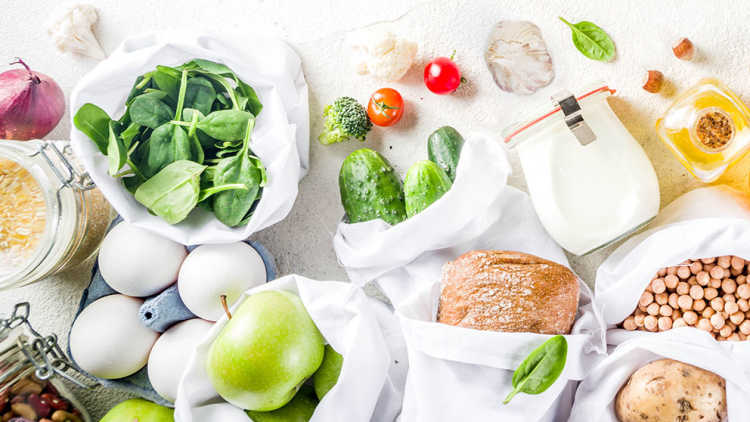
Inefficiencies and food waste can seem like an inevitable cost of doing business – but they don’t have to be.
Even low-tech, low-cost investments into a company’s technology and culture can improve both profitability and sustainability.
Food waste top priority
According to Cher Mereweather, President and Chief Executive Officer for Provision Coalition – an organization that works with food processors to implement sustainability strategies – product wastage is one of the most significant problems facing all Canadian food processors. By consequence, it also highlights significant opportunities.
Processors and manufacturers may not think their businesses generate a lot of avoidable waste, but the numbers suggest otherwise. In an analysis of 50 different Canadian food companies, Provision Coalition, along with partners at the Canadian Centre for Food Integrity and Wal-Mart, estimated 11.3 million kilograms of food products are unnecessarily wasted or downgraded annually.
Extra effort could mean extra revenue
Part of the issue stems from lack of recognition about what waste is and the impact of secondary markets. While lower-quality and damaged product, or that otherwise unsuitable for primary use, often goes to markets with lower profitability, Mereweather says a significant portion could have made it to the primary revenue stream with a little extra effort.
“What’s the true cost of the energy, labour and raw ingredients that went into making that product up to that point?” she says. “If you prevent it from going to secondary markets, that’s going to go directly to your bottom line. It’s product you can put in your package and sell.”
Small changes can make big differences
Nova Scotia-based poultry processor Eden Valley Poultry, which employs around 400 people, uncovered $95,000 in savings when they cleaned their chicken leg conveyor system one extra time during the production day. The cleaning relieved tension on chains and gears and reduced miscuts, which was a major cause of product loss on that line.
They also saved an additional $27,000 by installing a guard where thighs were separated from drumsticks. This closed a gap in the processing line and prevented chicken pieces from falling on the floor.
Dean Gurney, director of corporate social responsibility for the meat processor, says these findings better informed all staff of “the challenges and opportunities associated with food waste.”
Simple solutions to benefit energy use
For one of Ontario’s craft brewers, Cowbell Brewing Co., adding ceiling fans in their barn-style brewhouse reduced their heating and cooling load by a full 20%.
“The west-facing windows were coated to reduce the greenhouse effect by 80%. This, combined with software-assisted building design and placement, help maximize passive heating and cooling,” the company states, referring to other considerations given to the efficiency of its overall building design.
With around 160 employees, the company also takes advantage of its operational space by looking for sustainability opportunities in otherwise overlooked places, such as a pollinator and carbon-friendly green roof on top of the facility. The green roof also helps with insulating the building and improves stormwater management.
First steps
Sustainable solutions for food and beverage processors of any size don’t have to be expensive. Providing more or better training to staff and ensuring equipment is working properly goes a long way in reducing energy and water use.
“Sustainable solutions for food and beverage processors of any size don’t have to be expensive.”
Deliberately building a company ethos and goals around specific values is critical. It helps get employees on board while showing them their employer takes care of the environment.
More targeted investments can then be made, including improvements to facility layouts or incorporating more efficient and effective technologies (such as product sorting equipment using hyperspectral imaging).
But while higher-tech options can and do have an impact, the effectiveness still relies on the operator.
“Connect it to the why – why do we care? It’s about more than just saving money,” says Mereweather. “We have seen time and time again, you can have the best technology solution in the world, but if people don’t use it, it’s not worth a penny. Employees have to buy into the technology and be properly trained for it to be effective.”
Bring in experts
There are food sustainability consultants and engineers across the country who work with companies of all sizes to improve environmental and sustainability efficiencies.
Water and electricity efficiency consultants can advise on ways to cut usage. Energy audit inspectors will examine areas such as heating, refrigeration and cooling systems, facility processes, equipment and infrastructure. If it uses electricity, it will be part of the audit.
Meeting the need
Consumer demand is driving greener products, so it’s not an aspect of the business that can be overlooked without the risk of being left behind. And, as energy costs increase, looking for ways to trim spending is a smart risk mitigation approach.
Bottom line
Building a more sustainable business starts with taking a critical look at current technologies, activities and policies. Participate in an energy audit to see where to gain efficiencies in your facility – whether it’s with the structure itself or equipment upgrades. Also, look for ways to add value to what has traditionally been thought of as waste.
Article by: Matt McIntosh