How AI can help reduce food waste
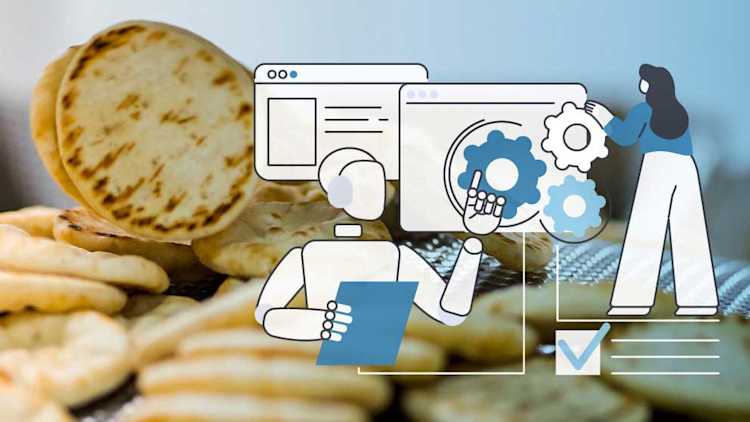
Artificial intelligence is booming, and the food and beverage sector is among the industries harnessing its power.
Randall Craig, CEO of Braintrust Professional Institute, says AI is producing a sea change across various industries. In the food and beverage sector, several key tools reduce waste by optimizing production and price and preventing potentially costly breakdowns.
Here are four ways to harness the power of AI to help reduce food waste:
1. Predictive analytics
An effective way to reduce waste is to produce exactly what your customers want, and predictive analytics is a key component in reaching that goal. It’s been around for decades, better known as forecasting, but AI has exponentially increased its capabilities.
“If you overproduce, you have spoilage, and if you underproduce, your customers penalize you. It costs you either way,” says Nestor Gomez, owner of Brightline Solutions. What AI brings to the picture is the ability to deal with large volumes of data from multiple sources.”
The cost-savings through improving forecast accuracy can be significant: just a 1% increase in forecast accuracy can save as much as $3.5 million annually for large-scale producers, Gomez says.
Moncton, N.B.-based Fiddlehead Technology describes itself as a blind spot analytics platform for food and beverage companies. They use deep learning to anticipate everything from customer to category and competitor actions. These tools can process a high volume of data to develop an accurate forecast of how much food to produce.
“They learn with data and become more and more accurate with the more data they ingest,” Gomez says.
2. Predictive maintenance
Equipment malfunctions can disrupt production and cause significant losses, but AI helps companies detect potential problems before they occur.
“If you’ve got a long history of understanding all the factors that lead to breakdowns, feeding those into AI could lead it to say, ‘Slow down the line’ or ‘You’ve got two months left,’” Craig says.
“Do maintenance at the optimal point with minimal disruption to your production line, which means your costs and spoilage go down,” says Gomez. Preventative maintenance plays a huge role in reducing waste.”
In real-time, Internet-connected sensors capable of measuring multiple variables, such as vibration and temperature, can identify a piece of machinery that needs repair or replacement before it breaks, enabling companies to prevent disruption and even enhance quality.
3. Cost optimization
Cost optimization is directly tied to reducing waste, Gomez says.
If you can predict a price that people are going to be able to afford for food products, you’re going to reduce spoilage and maximize accessibility immediately.
“If you can predict a price that people are going to be able to afford for food products, you’re going to reduce spoilage and maximize accessibility immediately.”
That’s particularly important in an era of volatile food prices.
For example, companies like Saskatoon-based BetterCart Analytics provide real-time and hyper-local price analytics to grocery retail companies, consumer packaged goods, and food and beverage processors.
According to company founder and CEO Melanie Morrison, BetterCart has more than five billion product records in its data and imports more than 38 million new product records from more than 3,600 individual stores and 25 retail chains each week.
4. Identify bad food
According to the World Food Programme, about one-third of all food produced globally - the equivalent of 1.3 billion tonnes – is wasted yearly. For most of human existence, detecting food that has gone bad relied on tried-but-not-necessarily-true methods: a delicate sniff or a careful prod.
But there’s also a lot of money to be made from all that wasted food, and it’s perhaps not surprising that a wave of companies is using technology to solve the problem.
One such company, ImpactVision, applies machine learning to hyperspectral imagery to detect imperfections, foreign bodies that could lead to a product recall or even internal defects that are not visible to the human eye.
Its machine-learning software has been trained to recognize what the company describes as structural similarities in food. It enables them to identify anomalies better and remove bad food from the system.
Article by: Chris Powell