Why a good potato storage facility is worth the investment
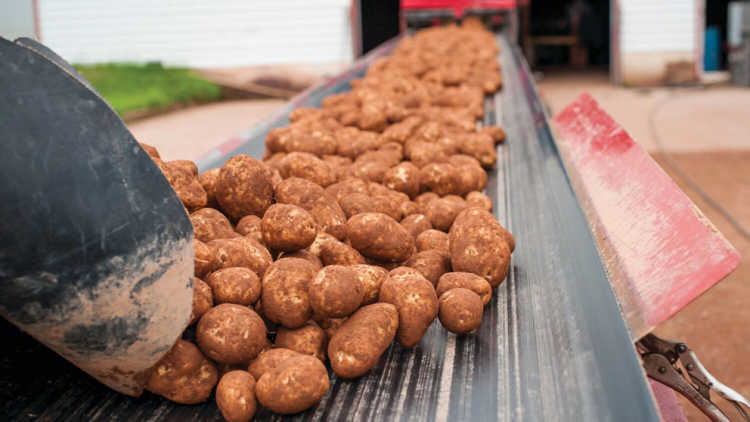
I recently visited a state-of-the-art potato storage in western Manitoba, a very large building with all the bells and whistles. I could feel the excitement and pride shared by the owner of this large facility as it promises to deliver everything a pile of potatoes would ever need to make it through the storage season in great condition and deliver a great quality product just-in-time to the processing plant.
“Just-in-time” delivery is not new, but necessary to adapt to new expectations of agricultural systems that will address topics like climate change, environmental impacts, sustainability, and export bans – all while improving quality and reducing costs in an ever-changing environment.
Is the considerable investment in such a facility justified? The answer to this question is “precision ag 24/7”. Agriculture has evolved and always adapted to new market trends, with producers having to deliver at the right place and time. This is as old as farming itself.
This spring, an export ban that affected PEI forced the producers to find a solution by stockpiling the spuds. To avoid a loss in quality, the utmost attention must be given to the potatoes during the post-harvest period. Therefore, building an efficient potato storage facility is not only part of effective risk management but also key to supporting and protecting the grower’s investment.
Over the last decade, an increasing level of potato production has been driven mainly by the frozen processing industry to maintain a year-round supply of high-quality tubers. Storage capacity overall has increased, as is the proportion of good storage facilities with improved environmental control. During harvesting season, from mid-August to early October, processors receive potatoes directly from the field. Outside this window, they source potatoes from storage facilities.
Overcoming challenges by building a state-of-the-art potato storage facility
Spuds are living organisms which produce heat through respiration and desiccation through both respiration and evaporation. Keeping this in mind, an efficient storage environment must be built if the tubers are required to be stored for up to 10 months. The goal is to maintain a healthy product by wrapping it in the perfect climate.
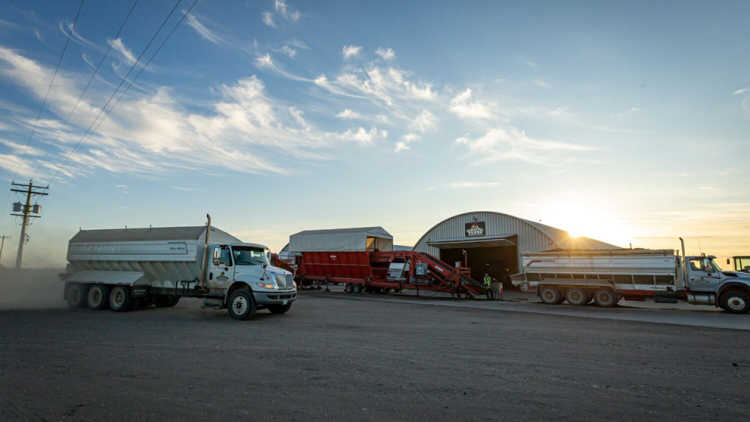
To meet all the requirements and avoid potato deterioration and post-harvest losses destined for fresh consumption or processing, potatoes are stored in large facilities under controlled environmental conditions.
They are kept in well-equipped large storage facilities at temperatures ranging from 2 to 10 °C, in a dark and well-ventilated environment with high relative humidity (85 to 98%) – these conditions will prevent rot and speed up the wound healing process of the crop.
Storage design – bulk storage vs. box storage
The main factors like structure style, insulation, ventilation/humidification and options such as auxiliary heating or refrigeration will impact the tuber’s health and quality.
Bulk storage
By far the most popular storage design, the bulk piled storage system allows producers to hold product longer with the highest quality. Generally less expensive, bulk storage product is held on the ground with air floor slots or ducts, including holes that feed the air up and through the pile. Options include internal or external fan houses. Air control through the product comes from duct-opening hatches that manually open and close.
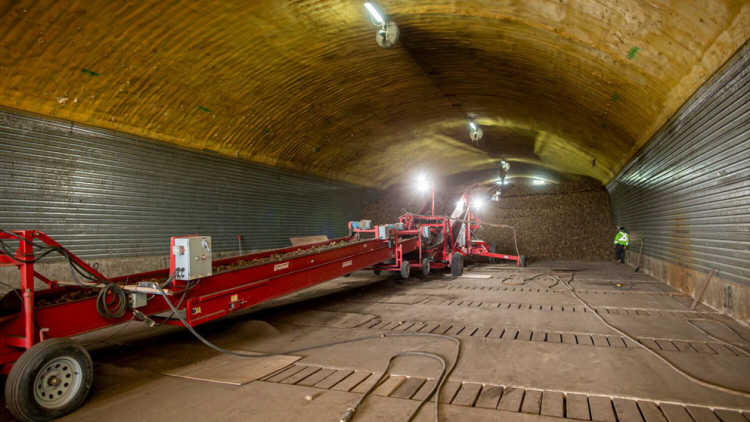
Image: Bulk storage bin.
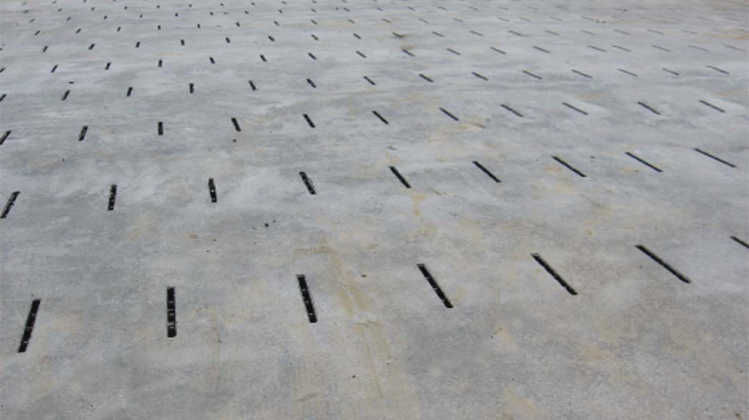
Image: Air floor slots or ducts, including holes that feed the air up and through the pile.
Box storage
Box storage is commonly used for seed and table stock. Although there may be differences, the boxes are typically 4’x4’x6’ and contain roughly 1500 lbs. of potatoes. The building is a steel structure, 26 ft in height, with 5 to 6 boxes on top of each other. Some facilities are built with full concrete walls, creating a long-lasting structure with a higher insulation value and better equipped for humidity control.
Box storage design feeds air through slots in the wall in and around the boxed product. Options include a cross vent and internal and external fan house. Letterbox design can also include cross ventilation or a consolidated fan house with a return air scoop. This way of storing potatoes minimizes the risk of contamination because it allows the removal of problematic boxes. Box storage involves much gentler crop-handling practices than those involved in bulk storage.

Structure styles
The most common storage buildings are concrete, wood stud, pole frame, and metal quonset. The factors that vary between the different building types are capital cost, durability, longevity and the type of insulation required for the exterior building envelope. The type of building used across the country also varies and is frequently influenced by climatic conditions found in an area.
An enclosed loading area at the front of the storage facility allows producers to comfortably load potatoes in severe weather conditions and minimize potential problems associated with chilled tubers.
Insulation
Storage must be properly insulated and sealed to maintain the environment required to keep stored potatoes healthy. Besides reducing heat loss and thus helping to maintain the desired storage temperature, insulation is also critical in preventing condensation. Condensation water dripping onto the tubers will encourage the development of soft rots and can significantly impact potato quality.
The insulation also impacts interior air quality. Insulation decreases the heat loss through the walls and ceilings, resulting in more heat of respiration exhausted from the building via the ventilation system. In extremely cold weather, this allows the ventilation system to bring additional fresh air into the building, thus maintaining adequate levels of oxygen and reducing the level of deleterious gasses such as carbon dioxide.
Ventilation
Ventilation is the most important factor for maintaining the storage shed's correct temperature, relative humidity and air quality. It is also essential for managing potential storage problems caused by disease or frost. The basic ventilation system design is similar regardless of the type of storage structure. A typical ventilation system consists of intake doors, fans, air plenums, ducts, exhaust louvers and a control system.
The size of the ventilation system component must be carefully selected to ensure that the ventilation air is evenly distributed throughout the storage facility. Intake dampers should be designed to close the return air supply proportionally as the intake door is opened. As more fresh air intake is required, return air carrying excessive heat or humidity will be forced out of the building through the exhaust vents. This is helpful when trying to remove excessive field heat at harvest.
Humidification
Under normal storage conditions, the relative humidity of the supply air should be maintained near 98%. Humidifiers should be installed immediately downstream from the fans. Three types of humidifiers are commonly used: high-pressure nozzles, centrifugal spinning disks and water-saturated fibrous media. The first two types are used less frequently as they are difficult to regulate, resulting in too much or too little water added to the air streams. The third type humidifies the air as it passes through a fibrous media without the pressure of free water droplets that can affect potato quality. This type of humidification unit will create resistance to the airflow and must be sized accordingly. The design of the humidifier is critical.
Heat requirements
The heat from potato respiration must be removed from the storage facility to keep the potato pile at the appropriate temperature. Warm air is exhausted, and a small amount of cool fresh air is blended with return air to keep the potato pile cool. The quantity of cool fresh air required for temperature control depends on outside temperatures. Under normal storage conditions, no auxiliary heat is required to maintain a constant pile temperature. However, there are circumstances where cool outside air above what’s required for temperature control is brought into the storage.
Refrigeration
Refrigeration should be available for any potatoes stored through the late spring and summer and can be an asset when trying to remove field heat during a hot harvest season. Refrigeration can be installed as a new, retrofit, temporary skid (mobile), or pad mounted and includes several different install configurations based on the need and applications.
Other features
New buildings are equipped with remote monitoring, heaters and CO2 sensors. These features help mitigate risk and allow more control over individual areas in the storage facility. It allows the producer to control certain areas where you might have some rot by applying more heat or cooling down a specific area where temperatures are elevated – all to keep a high-quality product and minimize any loss.
The addition of refrigeration coils, humidification units and light traps in the exhaust louver all impact the resistance to airflow and must be considered while designing the storage shed.
More advanced systems have a carbon dioxide (CO2) sensor that will activate the damper to bring in fresh air whenever CO2 levels exceed a pre-set limit.
Summary
The two-hour drive to western Manitoba was a good reminder that the most fundamental elements of a facility are not always evident at first. Storing potatoes presents various challenges. Having a large-scale storage facility with an optimal climate to avoid potato deterioration and achieve maximal tuber quality demands an extended understanding of potato storage management.
Tuber losses are inevitable when potatoes are not stored properly and can significantly impact the farm’s revenue. To prevent this, a good storage facility becomes a valuable farm asset worth the investment.
Article by: Peter Alder, Appraiser
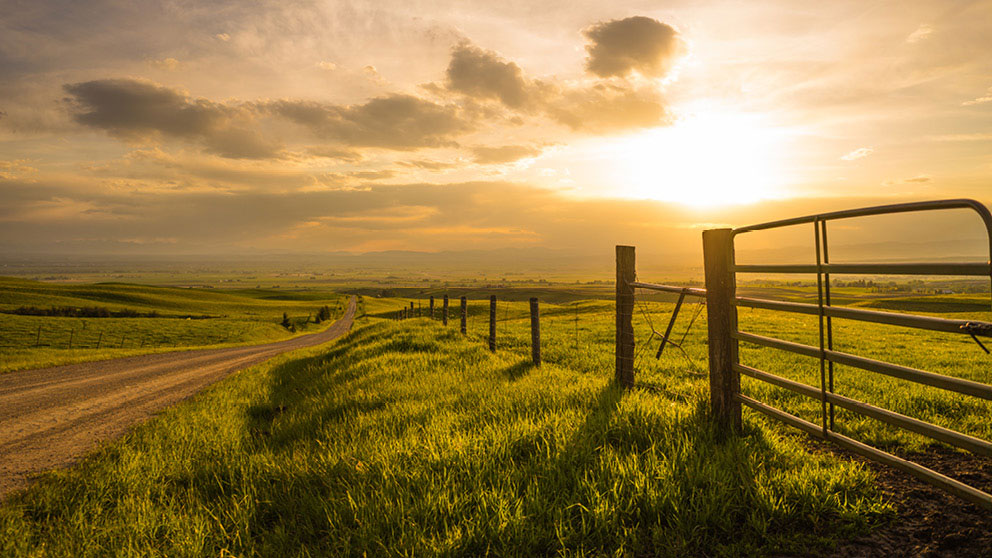
What landowners should consider when setting land rental price and agreement details.