Automation is here: How to get your processing business ready
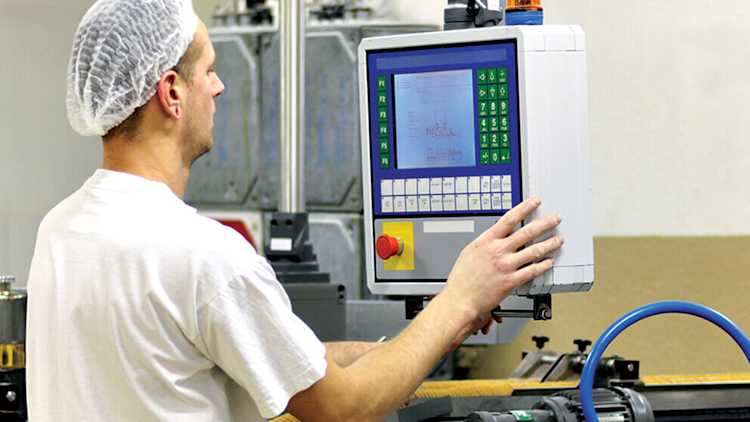
Imagine creating a production floor with fewer slowdowns, errors, safety concerns and other complexities.
Food and beverage processing experts in Canada say this is now a dream within reach for most, all with the help of automation.
Often used to reduce labour needs, automation also augments or supplements what humans do. Unlike robotics, which performs and replaces humans for repetitive tasks, automation can increase safety, reduce energy use, decrease waste, increase production and save space to get staff into higher-value roles.
Dana McCauley, Chief Experience Officer and member of the Canadian Food Innovation Network, wants processors to understand and access automation, which is still considered in its early stages in Canada.
“Right now, people who do want to invest in automation have a hard time finding a company to help,” she says. “There’s a lot to know, and there’s a ton of innovation, but getting it into the right hands is a little bit tricky.”
Make the time
Fewer trade shows and Canada’s size and fragmented industry contribute to the sector’s lack of knowledge and sharing. But being available to learn about new technology is a constant need, and if you don’t do it, “you may find yourself being a carriage-maker while everyone else is building a freeway,” McCauley says.
Be available to learn about new technology, or you could end up being a carriage maker while everyone else is building a freeway.
Anne-Marie Harte, an Industry Technology Advisor with the National Research Council of Canada Industrial Research Assistance Program, says automation can create efficiencies in production and help with quality assurance. A company that bottles hot sauce, for example, may spend time moving the product from bottling to crating. But, a conveyor and packager would reduce breakage, save time and increase capacity. Also, coding with uniform information may reveal undesirable skin on the product in some batches made with a certain pepper. Reviewing the data allows the processor to switch and improve quality.
Automation also allows businesses to be better positioned for the future. With the globe currently in Industry 4.0 – the fourth industrial revolution – the focus is on data, interconnectivity, automation, systems, business efficiencies and advancements. These are elements necessary to grow your processing business within constraints like labour shortages, supply chain challenges and competing in new market exploration.
Making it happen
The first step towards automation is reviewing the processes of your operation. Areas where slowdowns, errors, safety concerns and complexities occur help determine where automation can be most beneficial. Budget, space and staffing also need to be considered in the planning.
Harte has the following advice when considering automation in your production:
Consider where your biggest automation win is and build on it
Understand investment versus return
Create a staged implementation plan
For example, a food processor may lose the end of a product batch because of challenges getting the last of it out of the cooking vessel and into the packaging.
Stage 1
could be integrating automation from the product production vessel to packaging, saving time and marketable product.
Stage 2
could link the fill line to a conveyor belt that takes the product to packaging.
Stage 3
could include production elements to measure ingredients, blend the product and cook it.
Stage 4
could be scanners, computerized observation of power usage and equipment optimization.
Stage 5
could be a full reconfiguration to optimize flow.
Resources to help you plan
Information and programs through organizations like suppliers, provincial research facilities like the Saskatchewan Food Industry Development Centre, Canadian Food Innovation Network and National Research Council of Canada Industrial Research Assistance Program can connect businesses with the right individuals or even help create an automation plan. For example, the Saskatchewan Food Industry Development Centre does value graphing to identify the quick automation hits that create good ROI.
Dan Prefontaine, past president with the Saskatchewan Food Industry Development Centre expresses the importance of preparing now. “There’s opportunity if you look for it,” he says. “Automation might be a way to capture that opportunity. It may not be today. It may be five years from now. But you have to look towards it.”
At all levels of a food processing operation, labour can often be a challenge, and automation may move existing human resources into other higher-value roles. This transition can be the biggest bonus when staff shift to focus on optimization, growth and business success.
6 tips to help you automate:
Analyze current processes and bottlenecks
Build relationships with those in-the-know and ask for help
Know your objectives – reduce labour, improve food safety, increase capacity, cut costs, etc.
Approach in bite-size pieces with scalability in mind
Be specific about system needs when talking to suppliers
Get the right financing
Article by: Ronda Payne
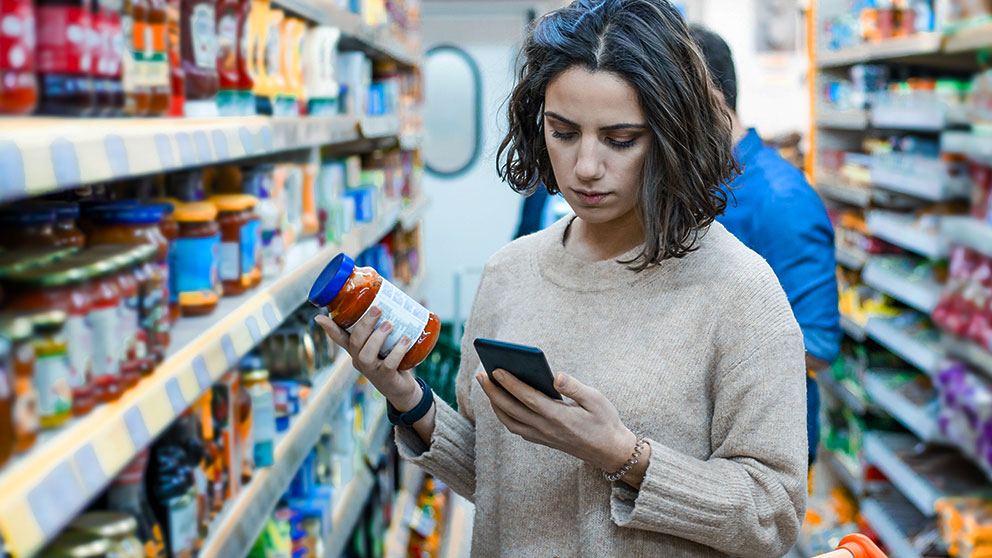
How to manage price increases while being transparent and keeping your consumer’s trust.